How Consulting Drives Digital Transformation and Operational Optimization
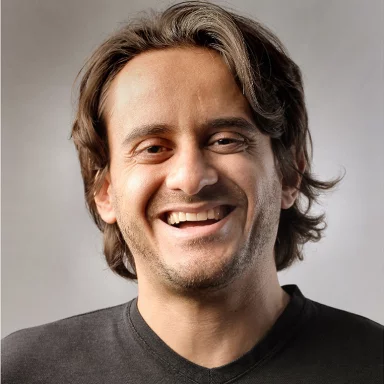
admin
In today’s rapidly evolving digital age, more and more businesses are facing the challenge of digital transformation. Many traditional industries, especially manufacturing, retail, and financial services, are under pressure from market changes, evolving customer demands, and technological innovation. To stand out in the competition, companies need to not only adapt to technological changes but also optimize internal management and operations.
Recently, a leading global manufacturing company sought the help of a business consulting firm to complete its digital transformation and optimize its supply chain management. The consulting firm was tasked with providing services including technology upgrades, process optimization, and employee training to help the company operate more efficiently and intelligently.
1. Designing and Implementing a Digital Transformation Strategy
The company had long relied on traditional production models and faced significant challenges in adopting digital transformation, such as employee acceptance of new technologies, system compatibility, and data management capabilities. The business consulting firm first conducted a thorough investigation and analysis, assessing the company’s current technology infrastructure and management processes. They then worked with the company’s senior management team to develop a digital transformation strategy.
Technology Upgrade: The consulting firm recommended a production management system based on cloud computing and artificial intelligence technologies, helping the company choose an appropriate software platform for implementation and data integration. By integrating smart devices and IoT technology, the company could monitor production line status in real time, optimize scheduling, and improve resource utilization.
Data Analysis and Decision Support: To enhance data-driven decision-making, the consulting firm helped the company build a data analysis platform to track market changes and customer demand in real time, thereby optimizing production plans and inventory management.
2. Supply Chain Optimization and Process Reengineering
The company’s traditional supply chain management model could no longer meet the demand for more efficient production and faster market response. The consulting firm implemented the following measures to optimize the supply chain:
Supplier Management: By introducing an advanced Supplier Relationship Management (SRM) system, the firm improved the efficiency of supplier selection, evaluation, and relationship management, reducing delivery times and inventory buildup.
Lean Production: The consulting firm applied lean production management methods to reduce waste, optimize resource allocation, and lower production costs. They helped the company adjust production processes to achieve full optimization from the production line to warehousing and logistics, ensuring efficient inventory management.
Automation and Robotics: Automation and robotics were introduced at appropriate stages of production, improving speed and accuracy, reducing human errors, and lowering labor intensity.
3. Employee Training and Cultural Development
To ensure that digital transformation and process optimization could be smoothly implemented, the business consulting firm developed a detailed employee training program. The training covered topics such as operating new technologies, using digital tools, and adapting to revised work processes. Additionally, the consulting firm assisted the company in fostering a culture shift, encouraging employees to transition from “traditional thinking” to “innovative thinking,” focusing on data analysis and intelligent decision-making in their daily work.
4. Results and Benefits
With the help of the business consulting firm, the company successfully completed its digital transformation and supply chain optimization, achieving remarkable results:
Increased Production Efficiency: Automation improvements led to a 30% increase in production efficiency, and product defect rates decreased by 20%.
Optimized Inventory Management: The implementation of lean production management improved inventory turnover by 15%, significantly reducing capital occupancy.
Smarter Decision-Making: The real-time data analysis platform enabled management to make quicker decisions, effectively responding to changes in market demand.
Enhanced Employee Capability: The systematic training program significantly improved employees’ ability to use new technologies and tools, increasing overall work efficiency and innovation.
5. Conclusion
This business consulting case demonstrates that digital transformation and operational optimization are crucial for companies to stand out in today’s competitive market. Through strategic planning, technology implementation, and employee training provided by the consulting firm, the company was able to successfully achieve transformation, increase efficiency, reduce costs, and lay a solid foundation for long-term business growth. This case also highlights the significant role that business consulting plays in driving technological innovation, enhancing operational capabilities, and strengthening employee culture.